In the last issue, LGLPAK LTD gave everyone a preliminary understanding of woven bags. Today, let’s take a look at how to store and maintain our woven bags.
First, understand the production steps of woven bags: extruding flat film, separating filament cutting, flat filament stretching, weaving, bag piece cutting, sewing, there may be various problems in each step, and the quality must be guaranteed during the production process. It is necessary to achieve the ultimate in details, and then LGLPAK LTD will lead everyone to interpret the details.
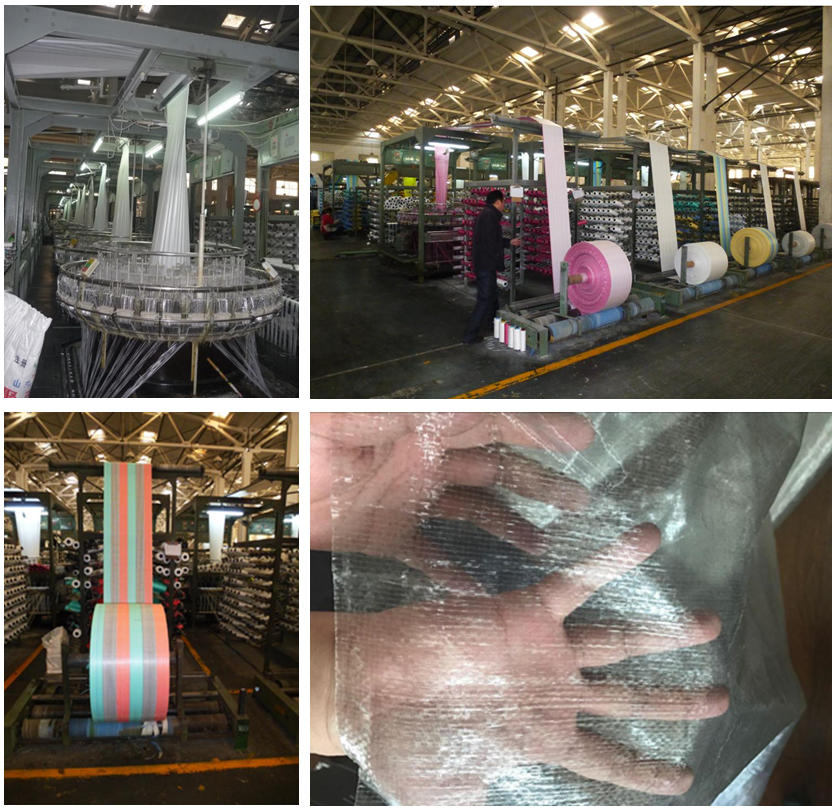
Uneven film thickness: Uneven film thickness occurs mainly because the position of the die and the abrasive tool is not level enough, which causes the temperature to be uneven and the film cannot be cooled at the same time. The cooling part needs to be adjusted to a horizontal position.
Film breakage: There are many factors that cause film breakage. Insufficient supply of pellets, too fast traction, clogging, impurities, too high or too low temperature, etc. may cause film breakage, which requires frequent inspection of material quality and cleaning Abrasive parts, adjustment of traction speed and temperature, etc. all have higher requirements for the quality and experience of the operators.
Serrated blank wire: The main reason for the serrated blank wire is the position and sharpness of the blade. In addition, if the cutting tension is insufficient or the film itself slips, this problem will occur. This requires us to pay attention to the inspection of the blade and the adjustment of the traction.
Flat yarn splitting or fluffing: Incorrect formula, uneven mixing of granular materials, and excessive stretching will cause splitting or fluffing. The raw material formula should be properly adjusted, fully mixed, and stretched.
There are differences between the weaving size and the expected size: there are many reasons why the size becomes larger or smaller: the tension of the weft becomes larger or smaller, the expander is too wide or too narrow, the flat yarn is too wide or too narrow, or the number of ends is too much or too little. This requires us to adjust the control weft tension components, adjust the width of the expander, adjust the width of the flat wire, and the number of ends.
Incision fluffing: Too high voltage and too slow cutting speed will cause the problem of incision fluffing. You need to adjust the voltage and cutting speed.
The thread breaks during sewing: The thread breaks during sewing may be due to insufficient thread strength, excessive sewing thread tension, excessive pressure on the presser foot of the sewing machine, and mechanical damage.
In the longevity process, every operation step will affect the quality of the product. Doing every step of inspection, maintenance, replacement, adjustment, and cleaning is the first step in quality control. In addition, it is necessary to measure the size of the woven bag, weigh the weight of the woven bag, count the number of woven bags, check the film, and check the printing during the inspection process.
LGLPAK LTD will continue to control the quality and bring customers the most reliable products. More friends are welcome to interact with us, and buyers are always welcome to ask questions.
Post time: Sep-10-2021